Fasteners and Machining: Improving the Production Process
Fasteners and Machining: Improving the Production Process
Blog Article
Navigating the Globe of Fasteners and Machining: Approaches for Precision and Speed
In the complex realm of bolts and machining, the mission for precision and speed is a continuous difficulty that demands careful focus to detail and calculated planning. From comprehending the varied array of bolt kinds to selecting ideal materials that can hold up against strenuous demands, each action in the procedure plays a pivotal duty in attaining the preferred result. Precision machining methods better boost the intricacy of this craft, calling for a fragile balance in between technical competence and cutting-edge techniques. As we dive into the methods that can improve both speed and effectiveness in this domain name, the interplay between quality assurance procedures and functional quality becomes an essential centerpiece.
Understanding Fastener Types
When choosing fasteners for a job, recognizing the various types available is essential for making certain optimal performance and integrity. Bolts come in a wide variety of kinds, each made for certain applications and requirements. Screws are used with nuts to hold products with each other, while screws are flexible bolts that can be utilized with or without a nut, depending upon the application. Nuts, on the various other hand, are inside threaded bolts that friend with screws or bolts, offering a safe hold. Washing machines are essential for dispersing the lots of the bolt and preventing damages to the material being secured. Furthermore, rivets are irreversible fasteners that are suitable for applications where disassembly is not needed. Understanding the differences between these bolt types is vital for choosing the right one for the work, ensuring that the connection is strong, sturdy, and trustworthy. By selecting the suitable fastener kind, you can optimize the efficiency and long life of your project - Fasteners and Machining.
Selecting the Right Materials
Comprehending the significance of selecting the right products is vital in ensuring the ideal efficiency and integrity of the chosen fastener kinds discussed previously. When it concerns fasteners and machining applications, the product choice plays an important role in establishing the overall toughness, longevity, deterioration resistance, and compatibility with the designated atmosphere. Different products provide differing properties that can significantly influence the efficiency of the fasteners.
Usual products used for bolts include steel, stainless steel, brass, aluminum, and titanium, each having its distinct staminas and weaknesses. Steel is renowned for its high toughness and sturdiness, making it suitable for a wide variety of applications. Stainless-steel uses excellent corrosion resistance, suitable for settings susceptible to moisture and chemicals. Light weight aluminum is light-weight and corrosion-resistant, making it suitable for applications where weight reduction is important. Brass is commonly chosen for its visual allure and exceptional conductivity. Titanium is known for its exceptional strength-to-weight proportion, making it excellent for high-performance applications. Selecting the best product involves considering variables such as toughness demands, ecological problems, and budget plan constraints to guarantee the preferred additional reading performance and durability of the fasteners.
Precision Machining Techniques

In enhancement to CNC machining, various other accuracy strategies like grinding, transforming, milling, and exploration play essential functions in bolt manufacturing. Grinding helps achieve fine surface area finishes and tight dimensional resistances, while turning is often used to create cylindrical elements with accurate diameters. Milling and drilling operations are important for shaping and creating holes in fasteners, ensuring they satisfy exact specifications and function appropriately.
Enhancing Rate and Effectiveness
To optimize fastener manufacturing processes, it is crucial to improve procedures and apply effective methods that complement accuracy machining methods. One vital method for improving rate and effectiveness is the execution of lean manufacturing principles. By lowering waste and concentrating on continual renovation, lean methods aid enhance and get rid of traffic jams process. Additionally, spending in automation technologies can substantially enhance production speed. Automated resource systems can deal with repeated jobs with precision and rate, permitting employees to concentrate on even more complicated and value-added activities. Adopting Just-In-Time (JIT) supply monitoring can also improve efficiency by making certain that the best products are available at the appropriate time, decreasing excess inventory and minimizing lead times. Furthermore, fostering a culture of partnership and communication amongst staff member can boost total efficiency by advertising transparency, problem-solving, and technology. By incorporating these approaches, manufacturers can attain an equilibrium in between speed and accuracy, eventually enhancing their affordable side in the fastener sector.
Quality Control Steps
Executing rigorous quality control procedures is crucial in making sure the integrity you can try these out and consistency of bolt products in the production procedure. Fasteners and Machining. Quality control measures include various stages, starting from the choice of raw materials to the last examination of the ended up bolts. This entails assessing factors such as material toughness, make-up, and stamina to guarantee that the bolts meet sector requirements.
Routine calibration of equipment and machinery is important to keep uniformity in production and make certain that fasteners satisfy the needed tolerances. Executing strict protocols for determining and resolving non-conformities or flaws is vital in stopping substandard products from getting in the marketplace. By developing a detailed high quality control structure, makers can copyright the track record of their brand and provide fasteners that meet the greatest standards of efficiency and toughness.
Final Thought
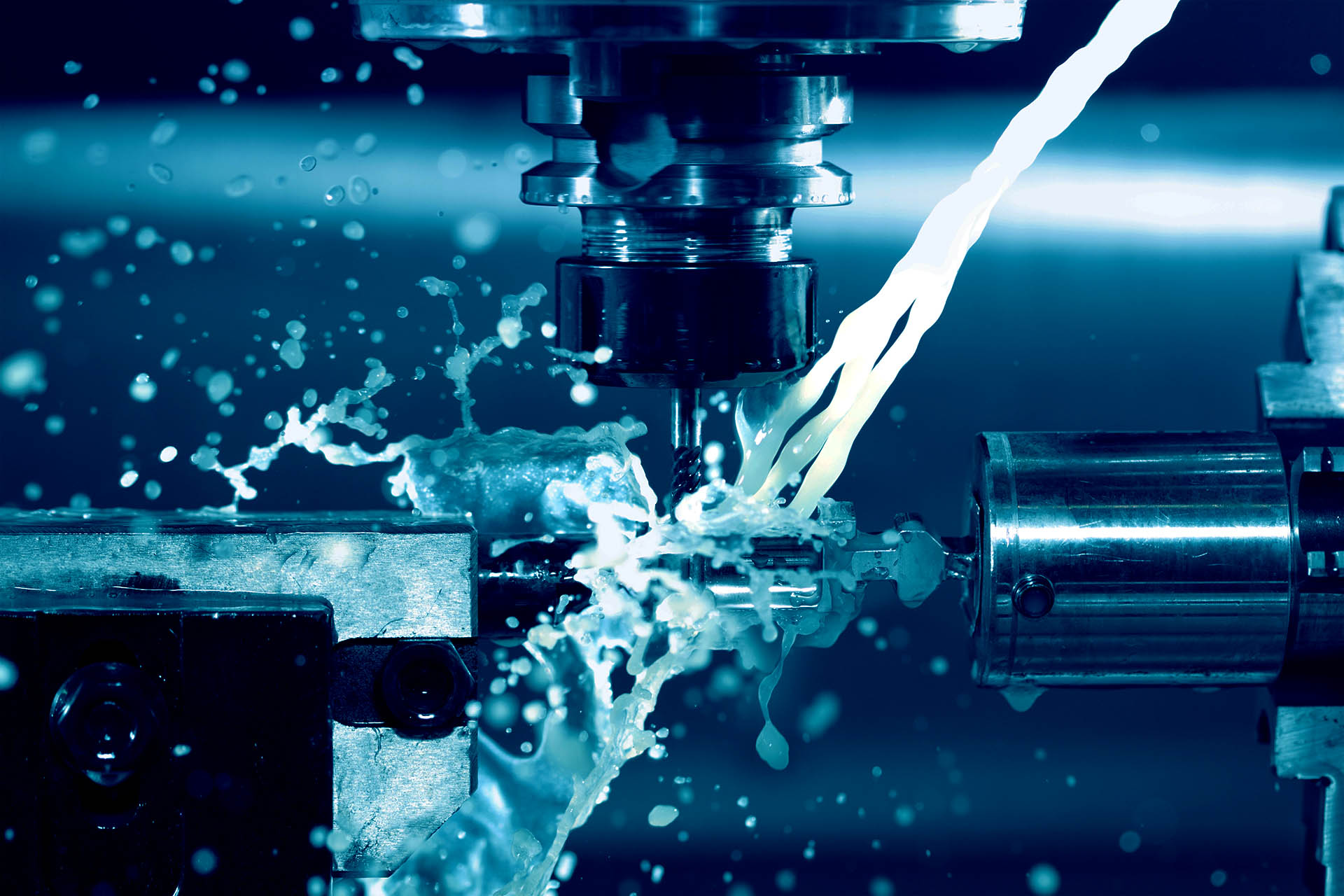
In the complex world of fasteners and machining, the quest for accuracy and speed is a continuous difficulty that requires precise interest to detail and critical planning. When it comes to fasteners and machining applications, the material option plays a vital duty in establishing the overall strength, toughness, deterioration resistance, and compatibility with the intended setting. Accuracy machining entails different advanced approaches that make sure the tight tolerances and specifications needed for bolts.In enhancement to CNC machining, various other precision strategies like grinding, turning, milling, and exploration play vital functions in fastener manufacturing.To enhance bolt manufacturing procedures, it is important to streamline operations and execute reliable methods that match precision machining techniques.
Report this page